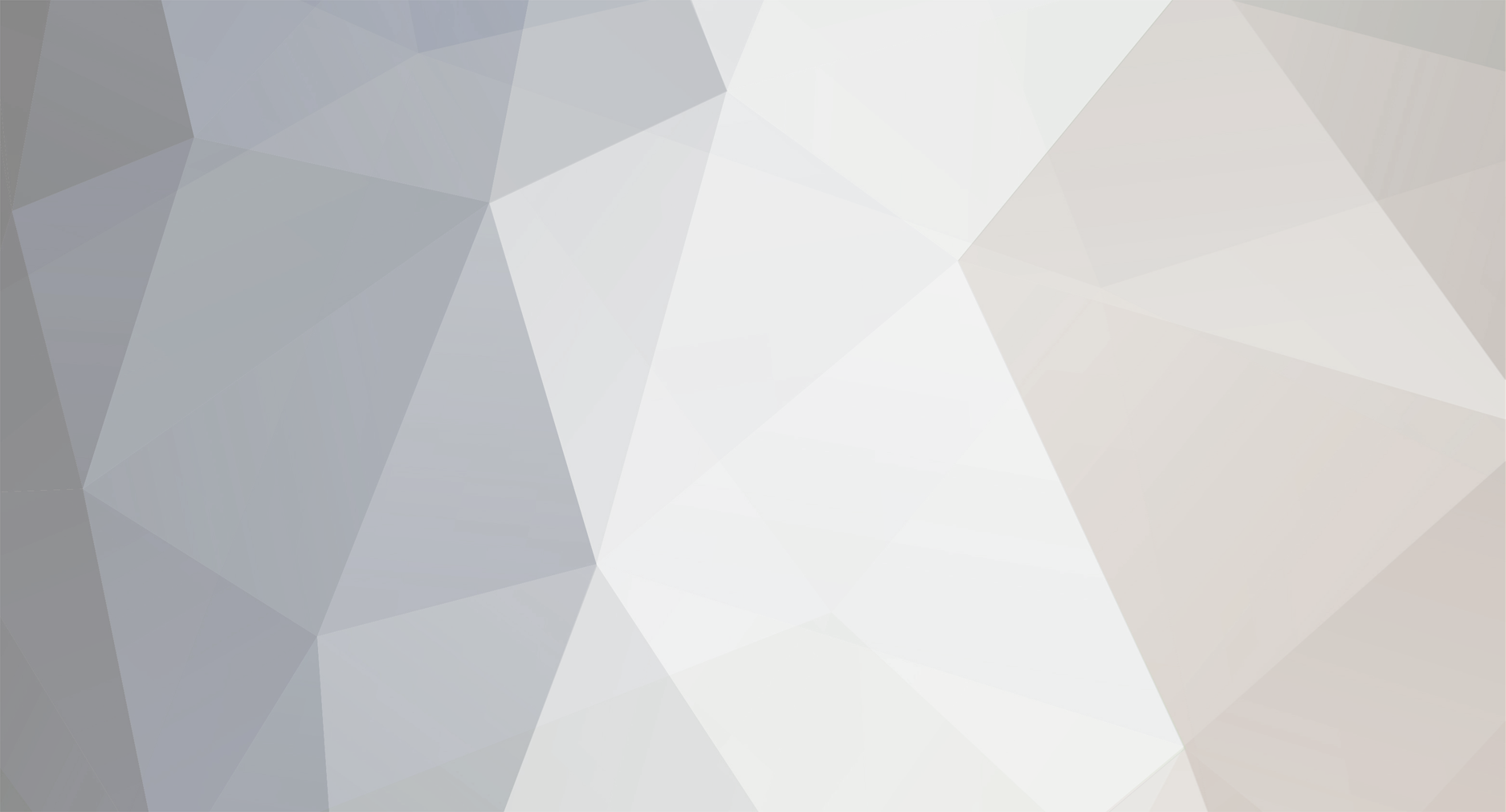
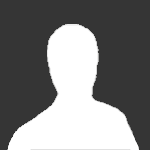
sc5.4
Members-
Posts
94 -
Joined
-
Last visited
Everything posted by sc5.4
-
No Flow And Cell Reversing On Jandy Aquapure 1400
sc5.4 replied to alwaysproblems's topic in All Swimming Pools Types
These flow sensors fail alot. With the system not recognizing any flow it will not turn the cell on. Mine acted up a few times before it totally failed. Changed it and now it works good. -
You sure the valve is opening when you turn it? Can you here the water draining out?
-
There is a few places online once you know the part number. I went with Discount Pool Mart. Click Here For Link
-
Found it online. My local pool store isn't to helpful with Jandy systems.
-
UPDATE: Found the Jandy Replacement Flow Sensor part number for threaded sensor is R0403700. Changed it out, and now I have FLOW and CELL ON. Just a note- when I changed it, I had the power off at the pool timer and at the main box to reset the 172 and 181 codes. When I powered the system back on the same codes and service light were still there. After a couple minutes the codes went away and panel showed normal lights again. Working like a champ now for 3 days.
-
My spa was doing something like that with the 2nd. pump kicking in. When I talked to the spa company they told me to shut off the main power and turn it back on. It worked for mine, it just had to reset the start cycle for filtering.
-
I found out today from Jandy that the screw on threaded sensors are the ones that the old cells have. The "new type" replacement cells are paired up with the non-threaded union sensors. I have been experiencing no flow at times. Cleaned the sensor and was ok for a while. Now, it's giving a 172 and 181 code. I need to see if I can test the front board diagnostics and determine if it's the sensor or board. I'm thinking flow sensor. I have seen a few online, just want to make sure before ordering.
-
I'm looking at replacing Jandy 1400 Flow Sensor (8ft.) Anybody know if the replacement is a threaded direct replacement? Also any advise on where to purchase?
-
I had the same problem 3 months ago. All the voltage tests were normal and DC cord connection good. Made sure the cell was clean, and still would set codes for 120-121. The thing is, it still was making chlorine while the codes were present. Then after a routine cell cleaning, I noticed the next day it was working fine with no more service light or 120 or 121 code.
-
I agree with Pool Clown. Don't hack stuff and have acid sitting around in the open overnight. If it's that far gone, buy a new cell and get it over with. It's like trying to charge a dead cell car battery and bringing it back from the dead.
-
oops! I guess it does look like that. I was thinking of more of a stand that can hold the cell without having to submerge it. THANKS for replies! On a side note, my cell has been working great lately.
-
No Flow And Cell Reversing On Jandy Aquapure 1400
sc5.4 replied to alwaysproblems's topic in All Swimming Pools Types
After showing NO FLOW for a week, now my 1400 has been working like a champ for a week straight. It must be the sensor acting up randomly. Again, the manufacture has been flooded with calls about flow sensors. When I called, it was like the tech knew what I was needing help with. I'm thinking of just ordering one now just to have on hand when it totally fails. -
No Flow And Cell Reversing On Jandy Aquapure 1400
sc5.4 replied to alwaysproblems's topic in All Swimming Pools Types
Thanks. Now if only Jandy could of told me that the other day. Waited forever on hold to ask them about how the display panel should read and if any changes or upgrades were made to the 1400 flow sensors. They said the sensor is the same as far as plugging in to replace old one. Right when I told the guy about the no flow on the display, he was quick to say "yeah... it's probably the flow sensor". Plus, you said that you replaced lots of them also. -
No Flow And Cell Reversing On Jandy Aquapure 1400
sc5.4 replied to alwaysproblems's topic in All Swimming Pools Types
That's right, when it first turns on it displays "wait" for a while. THEN it should display at least ON and FLOW correct? -
No Flow And Cell Reversing On Jandy Aquapure 1400
sc5.4 replied to alwaysproblems's topic in All Swimming Pools Types
Maybe these flow sensors fail more in hot weather. What's strange is, now that I have been keeping a close eye on my 1400's panel today, it didn't act up at all. Anytime the filter is on, the "FLOW" light should ALWAYS be lit when there is water flow correct? -
I have to find some type of plugs for sure. It would make it so much easier. Making a stand with a tube and end cap is a cool idea. It would be a more stable way to keep the cell from tipping over.
-
+1 on the expandable plugs. It's a more efficient way to clean the cell, and since you use less acid solution,(maybe a quart of 4:1) you can pour it in the pool when finished. Yeah...I'm going to try to find some that will work .Also I'm thinking of pouring bucket of mix in the pool that I just used. Wasn't much calcium settled at all at bottom of the bucket.
-
Excellent ideas. THANKS! Didn't find a cap to match up at the local HD store. I needed to clean it so I did the bucket soak. Turned out cell wasn't that dirty - I think sensor causing cell not to stay on long enough.
-
No Flow And Cell Reversing On Jandy Aquapure 1400
sc5.4 replied to alwaysproblems's topic in All Swimming Pools Types
I noticed CL production a little low so I cleaned the cell. After a while I checked the panel and wouldn't you know it a "NO FLOW' displayed on lcd. The only light "ON" was green power light. Hung out and watched the display for a few minutes and "Flow" light would come on with "Cell Reversing" light for about 2 seconds and go off. Then a few minutes later "Cell On" with "Flow" light and do the exact same thing, went off right away. I know it turns on cell and flow at times because everytime I walk past it I have a habit of looking at the thing! The panel was blank for a few minutes straight. No codes are displayed. I guess that explains the low CL. Is flow Sensor failing??? -
When acid cleaning cell, is it possible to just use regular 2" pvc caps on my 1400 cell without buying any special type cleaning caps?
-
Aquapure 1400 Errors - Is It Really Making Chlorine?
sc5.4 replied to ChrisR's topic in All Swimming Pools Types
Thanks Pool Clown. The "Boost" mode overrides this function for 24 hrs. correct? -
Aquapure 1400 Errors - Is It Really Making Chlorine?
sc5.4 replied to ChrisR's topic in All Swimming Pools Types
So... if you turn the system on for 2 min. or more then turn it off, then back on again. Does that make the system cycle all over again each time? This would be the case when back flushing the filter or vacuuming pool. -
I had to replace mine last year. The replacement was binding at times, so I sanded it evenly on both sides. The molded plastic seams on both ends had to be sanded flat to clear the walls on both sides of the skimmer. I was careful not to sand to much, and also I took some fine sandpaper and cleaned up the sides of the skimmer wall. The sandpaper block I used was the kind that is like a sponge type one that has sandpaper on all sides. Made a huge difference.
-
No Flow And Cell Reversing On Jandy Aquapure 1400
sc5.4 replied to alwaysproblems's topic in All Swimming Pools Types
Thank you Sly! I could of used that manual a few weeks ago while trying to determine what voltages should be at the cell. Mine is throwing a 120 code sometimes, and I'm checking DC cord and other connections. That service manual will definately help if other problems surface. Good luck with sensor codes. -
Technical Question About Chlorine Generators
sc5.4 replied to Bugman1400's topic in Swimming Pool Water Chemistry
Sounds like they are making cells bigger and better these days. Sorry to get off topic Bugman1400.