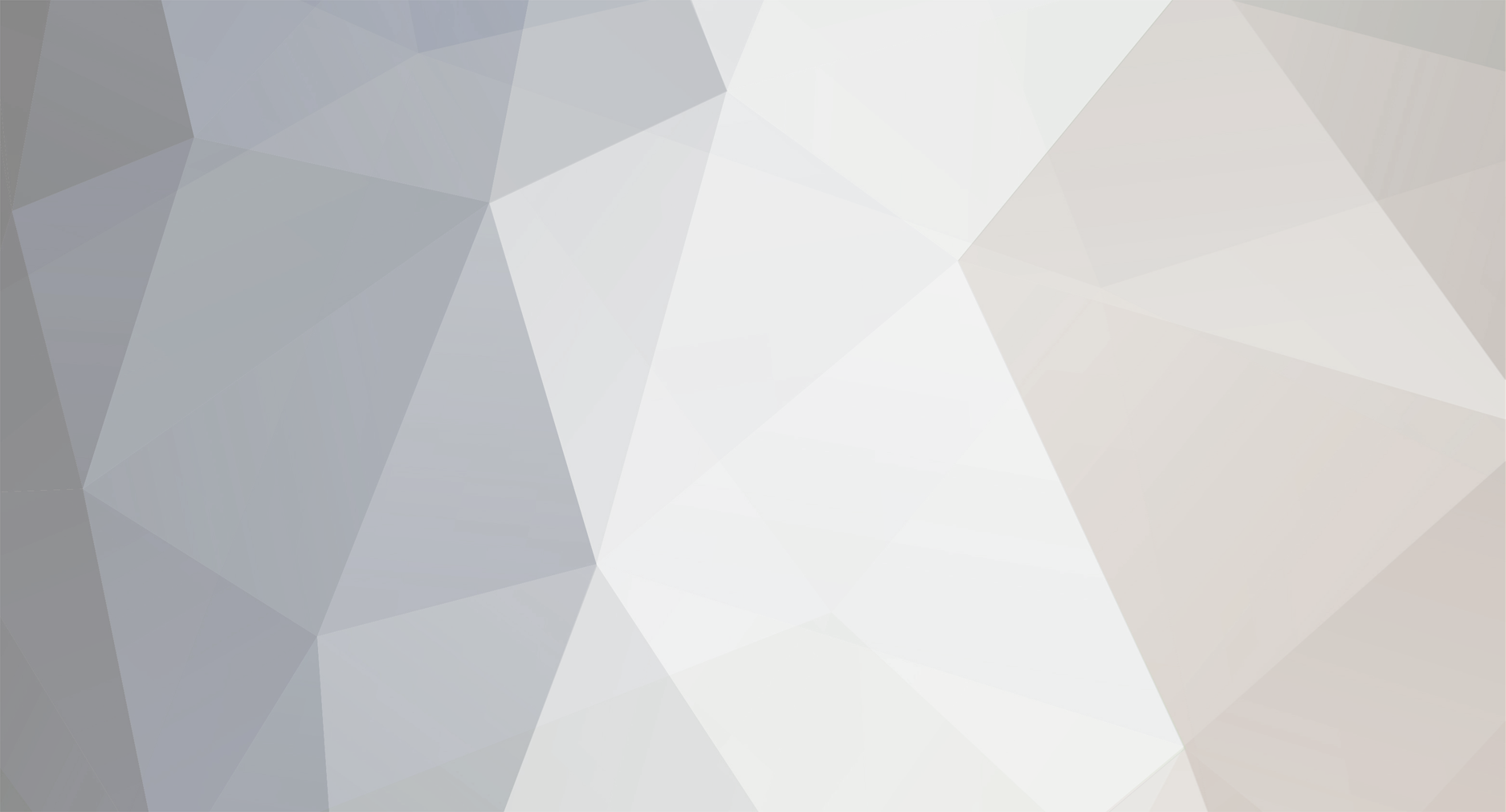
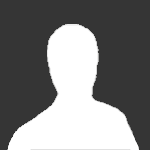
luey123
Members-
Posts
10 -
Joined
-
Last visited
luey123's Achievements

Junior Member (2/5)
0
Reputation
-
I have replaced the motor during this shake down along with the controller and topside. Each time the problem stayed constant. I think it's a bad contactor(s) mounted in an external box and/or the way my system is wired. An electrician is in order I guess but the previous 2 and a spa repair dude accomplished nothing. Fortunately, a few tries get her heating and we keep our fingers crossed while Winter sets in. My suppliers' way of coaching the electrician when they were here installing has me suspicious as does his observed disappearance from the web. Anybody have any poolspahelp.com experiences or stories??? thanks bk
- 2 replies
-
- Contactors
- shut down
-
(and 1 more)
Tagged with:
-
I turn to the best source of help available as to solving unique pool issues. Members have helped me greatly in the past and here I am again. A 2 year renovation on our 1400 gal redwood, vinyl lined, in deck hot tub is drawing to a close. It's been one long battle and for the time being we are down to one significant problem. My system shuts down about half the time when the in tub sensor calls for heat. This holds true whether in filtration or idle but seems less likely to occur if the jets are turned on first. When operating normally, I have hi-lo jets on my 2 spd pump, and heat functioning normally. When it faults, both indicator lights on my topside show jets and heat working but they are not. I have also noticed quite a variance in the temp of the pump motor at various times which is a puzzler... sometimes cool and sometimes too hot to hold your hand on. Equipment, all new : United Spas C5 controller w/ T7 topside, stand alone Raypak 11kw heater, Waterway 1.5 hp, 2spd pump, Our supplier guru (John at poolspahelp.com) coached our electrician on the use of a contactor box and the proper way to wire the system. At this point having replaced the C5 and T7 and sensor and pump, I'm figuring it's a contactor issue and/or the result of mismatched equipment from the gitgo although our tub DID operate flawlessly for some weeks. We are living with it for now worn down with one thing after another. If anyone has knowledge about how this system would be wired and whether or not a contactor could cause our problems, I would appreciate any input as to what may be the problem.
- 2 replies
-
- Contactors
- shut down
-
(and 1 more)
Tagged with:
-
I'm going crazy with having cracked and ruined the threaded pipe fittings on TWO Hayward C-250 filter housings while trying to plumb them. First issue could have been teflon tape but Hayward doesn't say not to use it and I was cautious about overwrapping and/or over tightening. The second time around with NEW FILTER I used Rectorseal 5 as per extensive research (Bowy it's a jungle out there on sealants and opinions!) and I can't even tighten beyond hand tight before the filter fitting starts fracturing in very very fine hairline cracks. I am suspecting some kind of thread variation or PVC differences but to my knowledge am doing everything right. I am shocked at the ease I was screwing the pipe in BY HAND with no sign of reaching "home" when the damn thing split... in numerous places!! aaarrrrggggghhhhhh!!!! Ive asked the dealer to contact Hayward but I have gotten much more help here if anyone has advice. Thanks.
-
I have a redwood hot tub flush built into an upper deck with a lower deck below. The tub pedestal support system below is surrounded by separate 2x6 framed walls on 16" centers that span from underside of upper deck to the concrete pad at ground level. It is all opened up presently for the rebuild which required removal of all the rotted material previously used... previous leaks to blame. What mat'l should I use for insulating these exterior walls in western Montana. We have moderately cold winters. I am going to side the exterior with as yet unknown mat'ls as I will need access to the tub for repairs etc and thought I would be fastening directly to the studs but am wondering if I shouldn't insulate over the studs instead of between them for a better result. Any suggestions would be much appreciated.
-
Thank you. Duly and sadly noted. We experienced other issues with our supplier too. We were very thankful to have their (the only) internet illustrated guide to relining/rebuilding an old redwood tub on the net but the thanks we showed by ordering the liner and equipment from them was misplaced. It's a damn shame since we were ordering new, starting from scratch and asked for their "Professional" advice in selecting everything. I have some other questions and need for input but am going to post a new topic. Thanks again.
-
I have had success this time around with the pressure switch adjustment and am very thankful for the mentoring. I had an experience related when it dropped to 45 degrees here in MT the other night and I awoke to an "FR" readout on my topside control. The cause evidently was the unused high temp probe from the controller also governs freeze protection (news to me) and being disconnected from anything, picked up the ambient temp and kicked her into freeze protection mode. I taped it to some of the pvc plumbing to reflect water temp to the controller but wonder WHAT I SHOULD REALLY DO WITH IT along with the unused pressure switch wires coming from the controller. Granted, I have both protections active separately in the heater but is it OK to shunt the unused pr sw wires together and leave the high temp probe taped to piping the way I have it now? We are enjoying the new rebuild a lot. It is 1200-1300 hundred gallons and we purposely left the furniture and/or any obstacles out of the mix. It is very nice all opened up.... an 8 foot pool about 40 inches deep. We now have to insulate the 10 x 10 pool house and pedestal below as well as flash the topside under the deck to shed the water away from the walls below. Call in engineering please!!
-
Got it. Thank you. The thumb wheel on the built in switch is ungodly stiff. The slight movement of it did not sway the ohm meter much then it would go nuts. Back and forth with no real feel for the sweet spot. It is new too. I followed some fairly good instructions for adjusting it found on a site until the last couple steps when clarity left the procedure. I will look for related mat'l here as to proper adj without power. I aint goin in WITH... Thank you kindly. Much appreciated.
-
I have adjusted it and may still need more calibration but I'm bothered by the shunted pressure leads from the controller and unused hi limit probe. Is this separate contactor for the free standing heater a commonly used config? It's done to save amp draw on the controller I believe but is it Kosher?
-
Man, way to shred a newbie. Feel better? I didn't know equipment could vary so much in a pretty basic layout. Controller is a United C5 stand alone with T7 topside control. Heater is a 14.4k Raypak. All I know about the setup electrically is that a separate contactor was needed for the heater. I have a topside cutoff and two breakers in the panel.
-
I have an 8' in-deck redwood hot tub that I've recently refurbed including plumbing, all components and equipment along with new electrical wiring professionally done. I've had no luck with the supplier of my equipment as to my problem and so am asking for help here. I have a stand alone 14k heater that is supplied power via a separate contactor and not the controller. It has it's own pressure and overheat switch in addition to the controller wiring for a duplicate p switch and sensor. Presently there is no connection/interface between my controller and heater as the controller p switch wires are shunted together to fool the controller. I've adjusted the p sw. in the heater to adjust for the increased pressure due to tub being above pak. I have about 3 or 4 lbs of pressure with pump off. Problem is:: Overheat switch is kicking out on heater unless I keep filtration on constantly. Is there a way to let these switches operate in synch or wire controller directly to heater?