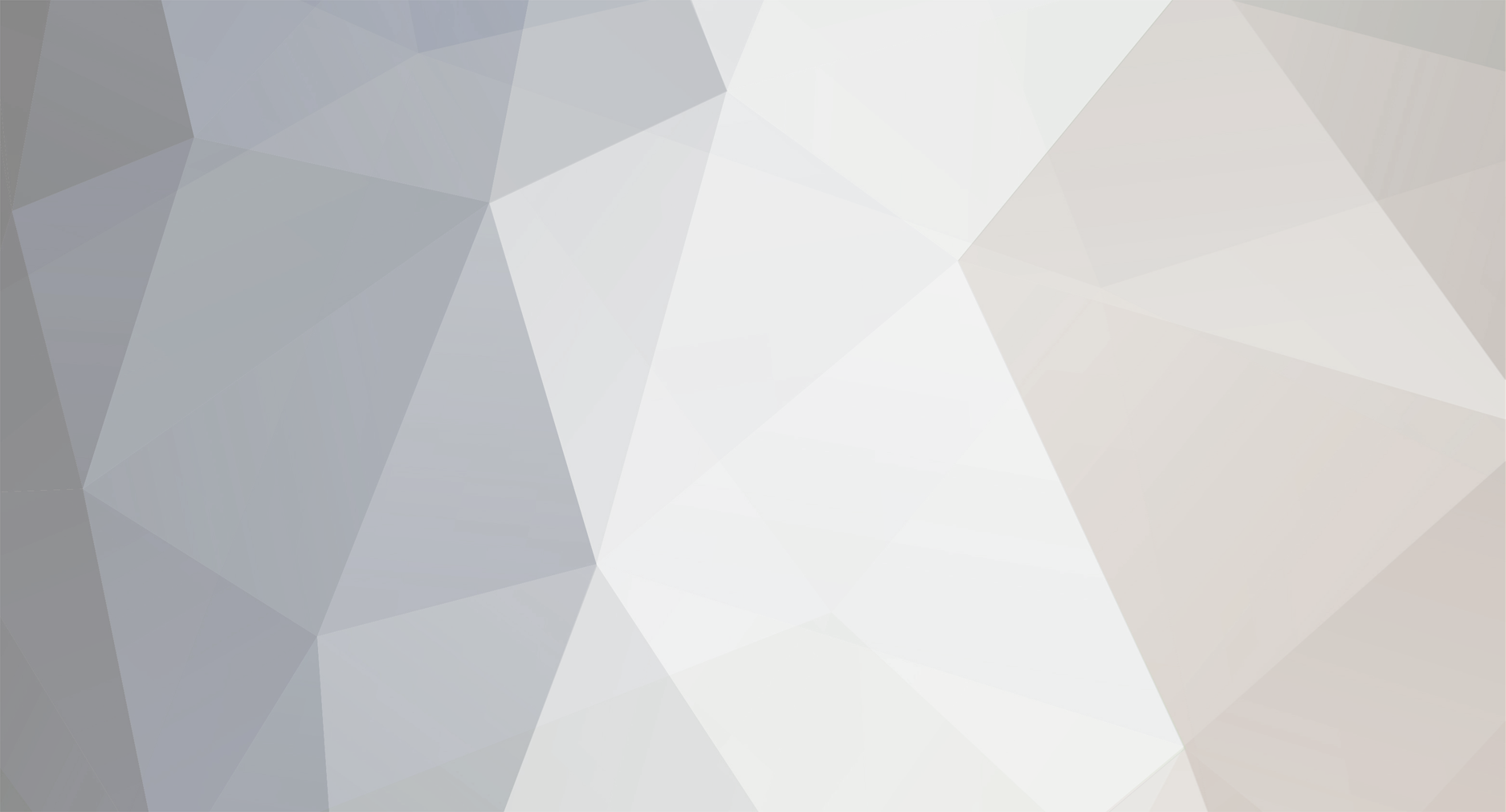
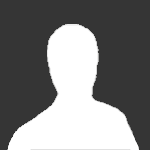
Bugman1400
-
Posts
218 -
Joined
-
Last visited
Posts posted by Bugman1400
-
-
Does your vacuum line have a clog in it?
-
Valve 4 should be turned 180 degrees. You should be good to go after that. Also, does your SPA spill over into the pool?
-
I have a liner pool that hasn't been replaced yet because it is in good shape. However, several of my neighbors have had their liner replaced to the tune of $2500. It takes a special expertise and a professional pool company to do. So, call your local reputable pool company and let them judge if the sides are too deformed. Even if they are, I'm sure that is something they can handle. I really doubt you would need the whole pool rebuilt.
-
I've had the Dolphin for years. I love the cleaner but, hate the cloth diaper I have to clean (spray off with the hose) every 2 or 3 uses. However, it cleans algae better than any other cleaner. It is important to know what type of pool you have. I have a liner and the Dolphin works great. Also, I have many large trees that over-hang the pool so, I get a plethora of leaves (large and small), twigs, and dirt in the pool. I've also been know to lose touch with my pool chemistry once or twice during the Summer and the Dolphin will help lick the algae off the side of the pool.
Cheers!
-
Is your ignitor an HSI (Hot Surface Ignitor)? If so, are you saying that it does not glow during the startup cycle? If not, then most likely you have a safety switch issue. Look at the wire schematic on the door and check the chain of safety switches. There should be a pressure switch from the exhauster, a couple of thermal switches from the heat exchanger. Since the heat exchanger has the pool water circulating through it, one of the thermal switches may have rusted. Thats what happened to me last year.
-
If it is done before the GFCI, it usually is not a problem as long as the load when the stolen 120V doesn't cause an excessive current draw on the feeder line. This is usually seen is portable spas. I prefer to see it done right though, two 120V legs, a common and a ground feeding the sub panel. A 240 breaker(s) to the pump(s) and heater, and 120V breaker to the other devices, be they the board's transformer(s), lights, outlets, etc... Keeping everything separate just makes troubleshooting that much easier, especially for the next guy that sees it.
Scott
How in the world can a 120V leg be stolen post GFCI.....if the GFCI is operating properly? In theory, this does not seem possible since GFCIs operate on milliamp difference. It seems to me anything operating at 120V off of a "stolen" leg downstream of a GFCI would cause the GFCI to operate immediately because of the return current on the 120V through the NEUTRAL would not be returned through the other 220V hot leg.
Please explain.
-
So I recently had a Super II go out. No big deal right? So I go to make the repair, and the power center is not the typical nice neat orderly electrical installation I'm used to seeing (17 wire nuts, are you tracking with me...).
As I'm removing all the birds nest of wire and "doing it right" I see that the installer has stolen a leg of 220v from one of the line sides of a relay (power for the control board/transformer) and tied the neutral back to the line side of a GFCI. Naturally I run a hot and a neutral from (not through) the GFCI to the transformer and resolve the short cut the installer took to save 20" of copper. Naturally I thought to myself... Lazy installer.
(different pool) Two days later while tracking down a broken leg of 220v I notice that intermatics wiring diagram has the very same "theory" to wire a 125v time clock on a 220v system, just take a leg from the line of 220v and run the neutral back to 110v. Of course you're going to ask which intermatic, and I'll get you that info, but this simply doesn't seem like a good practice? I have purchased a 220v time clock to replace the 125v clock and intend to wire it properly.
Isn't it true that if you steal a leg from 220v, then the load on that 220 system is unequal. And couldn't this difference, even though small, cause problems in the long run.
So what is my question... Did I overkill by correcting the problem or is this a common/acceptable way of wiring 110 when 220 is present? Anyone have experience with seeing it done one way or the other.
I'm a bit confused by your question of stealing a leg from 220 causing an imbalance. This practice is done all the time in 220 devices that also contain the neutral and 110 devices. This allows the 220 L1 & L2 to supply the 110 (L1 or L2) to the 110 devices inside the 220 device (like contactors, fans, displays, etc.) This will cause an imbalance across the 220 but, does no harm at all. As a point of reference, half your house 110 outlets and lighting is wired on one leg of 220 and the other half is wired to the other leg. So, you could easily have half the house using the power off just the one 220 leg without any ill-effects.
Make sense?
-
Got any pictures?
-
The schematic indicates that there is a blower capacitor. Although, I don't recall one on my LT400. You didn't say what model your heater is. If you do have the capacitor then that is likely the culprit and may need replacing. First, use some pliers to pull the terminals off the cap and re-seat them and see if that helps. if not, get another cap from the pool store or HVAC store (not Lowes or HD).
It is not the transformer.
-
Can anyone tell me if I need to seal the Jandy valve (with 8 screws) with silicone or anything? I had to remove it for the 1st time ever after the Drain King (hose bladder attachment) shot off the hose into the plumbing. The top of the jandy valve was on really tight, and I had to pry it loose with a screwdriver. Now that it's all put back together I think it might be sucking in air. Should it seal with just the screws or does it need something additional?
I am suspicious there are leaves blocking the plumbing somewhere still. I am going to try using an air compressor to blow out the line since the Drain King didn't clear it. A couple of weeks ago after a lot of wind we did get a lot of leaves in the pool, and I discovered the pump basket with more leaves than I've ever seen before. It was shortly after this that we noticed problems with the pump not priming.
Again, should I replace the o-ring on the pump basket area if it looks/feels ok, but has never been replaced in 7 years? Or is it probably ok?
One thing I've noticed when I prime my system is that it seems to prime better when my valve is set on WASTE instead of FILTER.
If you suspect the Jandy valve then perhaps you can put plastic over it and tape it up and see if the air is sucked out of it when the pump is on. Also, change your lid gasket. The gasket gets compressed over the years and makes it easier to put the lid on. If the gasket is new, the lid should take more of an effort to close.
Let us know what you find.
-
The only number we are missing is what you pay in electricity per kilowatt-hour or megawatt-hour. You should be able to figure it out from your electric bill.
If your rate is around 10 cents (USD) per kilowatt-hour, well, you can see that you're spending about $2.50 USD a day, $75 a month.
-
New: Drill 3/8" hole in the pipe between the pump and filter and clamp in place. Run the cord into the low voltage raceway and secure its path to the existing conduits as needed. Connect it to the appropriate terminals.
Its a 10K thermistor but I don't remember the rise and fall rates compared to the temp.
Scott
The drill hole size is what I needed most.
Thanks!
-
Does anybody have the instructions for the Jandy 7790 Temp Sensor? Also, how about the resistance chart?
Mucho grassyass!
-
Yes, WhisperFlo WF-26.
Curve shows 67.5 feet head loss @67.5gpm (filter in-line), 50 feet @90gpm (filter bypass). So the filter brings me a loss of 17.5ft, which is 7.6psi. Now the math gets fuzzy (if it isn't already). Curve for the filter shows 4psi loss @67.5gpm. Who knows what the difference between the 7.6 and 4 means, especially since I'm using a multiport valve that's got all sorts of different restrictions, from position to position.
Back to the question, at 67.5gpm, based on curve G above, I'm really in the sweet spot for pump efficiency (by chance).
I don't think it is by chance, but by design. I think the difference between 7.6 and 4 is measurement error. For example, you indicated 50ft.@90GPM, but I read it as 48 or 49ft.@90GPM. Add up all those error rates including reading you Blue & White and you'll see why the true number is hard to calculate. Perhaps, this pump is pumping against a higher head pressure than your last pool. All in all, everything seems good.
-
Sounds like a nice toy....wish I had one. Although, they don't seem too expensive....maybe I'll get one.
What is your flow rate in Recirc mode (DE filter bypassed)?
Also, what is the spec'd flow rate of the pump?
-
Another question....how are you getting your flow rate?
-
Chemicals are in balance, and it's a brand new filter, so nothing to backwash. I had it running with empty media, no DE in there at all, until the first charge today. It's a 1.5hp (1.1sf) pump.
We moved in to this house over the summer, but haven't had the time to play with it as much as I'd like to have (yet); all the individual pressure side and vacuum side lines at the pad are individually-valved, so I can experiment a bit- my guess is that the vacuum-side lines are pitifully under-sized and that's what's restricting me- especially since I'm convinced one of the two skimmer lines is clogged. My previous pool had a 2.2sfhp pump and pushed 110gpm through a 420sqft cartridge filter... but I digress, different conversation.
So, then, it IS normal to not see a pressure increase from naked (no DE at all) media to properly-coated? Again, initial startup on a brand-new filter.
I think what PoolGuy was referring to with running the filter without DE is that......you are sucking all the dirt and debris from the pool to your naked grids during the time you were getting your baseline data point. So, if you added DE after that without backwashing then your DE is now on top of your dirt and debris.
I'll ask the next question.....what is the size of your plumbing?
-
A call box should disable L1 and L2 to the pump. Failure to do so can result in the motor being damaged. A 120V call box would only disable L1. A 240V call box should do both.
Scott
It is a 240V call box, but according to the power company this is how they always hook it up. Like I said before it always hooked up this way, timer is now new and so is the call box... So it just leaves the motor.
Removing one leg of a simple 240VAC device is a common way to stop a motor. As far as variable speed drive motors, that is completely different. The motor is not driven directly from L1 and L2, it is driven from the variable speed drive circuit. As far as safety, obviously, you would need to completely isolate all voltage to replace or work on the motor, but for normal operation, switching one leg is common. If you have a pool heater, you can look at how the exhaust fan is switched with the Fenwal.
As I said before, I am very familiar with call boxes (load controls). It is basically, a relay ON/OFF switch that receives a signal through the power line to turn OFF or ON.
Finally, I do not want to get into a pissing match with Pool Clown or PoolGuy. They have already forgotten way more than I will ever know about pools and both have my most utmost respect.
My pump is not a variable speed... So if its a common way to stop a 240VAC motor is to cut on of the leads, and now that is not happening, what could have changed in the motor?
If you are electrically inclined, I would advise checking the voltage at the motor terminals with a voltmeter and make sure the voltage at the terminals is within 5% of what is on the nameplate. If it is, then check the cap; as I pointed out before. If you are not electrically inclined, then call somebody. That cap can hurt.
Let us know what you find.
-
Removing one leg of a simple 240VAC device is a common way to stop a motor. As far as variable speed drive motors, that is completely different. The motor is not driven directly from L1 and L2, it is driven from the variable speed drive circuit. As far as safety, obviously, you would need to completely isolate all voltage to replace or work on the motor, but for normal operation, switching one leg is common. If you have a pool heater, you can look at how the exhaust fan is switched with the Fenwal.
As I said before, I am very familiar with call boxes (load controls). It is basically, a relay ON/OFF switch that receives a signal through the power line to turn OFF or ON.
Finally, I do not want to get into a pissing match with Pool Clown or PoolGuy. They have already forgotten way more than I will ever know about pools and both have my most utmost respect.
-
Thanks. So whats happening is removing the load control of course fixes it. When its connected and the timer is in the on position it works when the timer switches off, L1 has no power but L2 which is connected to the load control box is still getting power and still flowing to the pump, so its half on. Again this just started happening. I have replaced the timer and had the power company replace the load controller, same issue. The only thing left is the pump.
Does anyone know the inner workings of these pumps? are there any devices in the pump it self that could be causing this?
Electrically, the pump is just a motor. There are many things that could be causing excessive heating. If the motor is not any louder than normal then the bearings are probably not the culprit. The next thing on the list is to check the capacitor. Sometimes, the terminals get loose or oxidized and result in a high impedance connection. The first step is simply pull the quick disconnect terminals off with pliers and re-seat. Then check to see if that solves your problem. If not, the next easiest and cheapest way to go is to replace the capacitor.
-
If you take the call box out of the circuit, and the motor does not get hot and trip the breaker, i would come to the conclusion that the trouble is the call box. I realize you have had someone out to check the call box, and i have this to say: It's easier to say it's some other components fault and not have to replace or diagnose said call box. Ask them to humor you and just replace the call box.
Completely agree, took the call box out and hooked up the pump properly to the timer, works just fine... they did replace the call box, same issue. And like I said this use to work fine, and then one day with no one touching it, it stopped working fine.
I have another possibility. Working for a power company, I am very familiar with load controls (call box). Load controls are normally installed on 240VAC devices (water heater, HVAC condensor units, etc.). For your 240VAC motor, it should not matter if L1 or L2 is removed. It is impossible for power to flow. If L1 is connected and L2 is not, where would the power flow to? This is the principle as to why it is connected the way it is. Your description of the connections sounds correct. For the company I work for, it is unusal for the load control to be used (only at the very worst peak times (ie Summer on 99 deg days)). However, the power company still gives the $8 credit to the customer during the seasonal times of the year for the extra insurance.
It is quite possible for you to bypass the load control without the power company ever finding out......many folks do. It usually happens on 99 deg days when the power company needs the extra power, but people discover that their HVAC unit is off on the hot as hell day and the desire to save $8 goes out the window.
It is possible that your motor or some component thereof (ie cap) is going bad and causing excess heat. There could also be a bad L1/L2 connection causing reduced voltage at the motor terminals that may also cause overheating.
Pool Clown has the right idea by eliminating the suspects one at a time. Eventually, you'll find out that it was Professor Plum in the Library with the candlestick.
Let us know what you find.
-
If you are getting certain new or not seen before displays on the new LCD, that board is either wrong, or like Scott says there were revisions that changed the display and is now the correct replacement. By the way, what model is this heater?
I'd like to see some pictures.
-
Motors wear out. Replacing the motor and seal set is not hard. Some replace bearings in the motor but I find motor swaps last far longer.
Scott
Is it easy to pick up a motor and are these usually quite cheap? I've read a bit about replacing the capacitor, but unsure exactly how this would help in an overheating sense.
Motors can overheat for a variety of reasons:
1.) Excess load.....perhaps something cinching down on the shaft for whatever reason.
2.) Reduced supply voltage.......makes sense, lower voltage means more amps have to be used to get you to 1HP. More amps means more IR losses through the windings and higher temps.
3.) Bad or failing cap........a bad cap or cap that is starting to fail will not provide sufficient torque for the motor to drive the load. A bad cap could be a good cap, but bad terminal connections. So, the easiest thing to do for this one is to pull the quick disconnect terminals off the cap and re-seat them.
4.) Bad or failing bearings.....I have seen many bearings fail or start to go bad. Usually, the motor gets much louder. It is easy to see that failing bearings can result in additional drag on the motor (excess load) because of the metal to metal contact. Like I said before, usually, the motor gets louder.
-
What do the 1&2 terminals (Low Voltage Heater?) do?
Jandy Lxi Heater Won't Start!
in All Swimming Pools Types
Posted
If you are not getting the exhaust motor to blow then check it.......it could be seized. I usually check these by disconnecting all power to the unit and then use my screwdriver to see if I can manually turn the fan blades. If it won't turn, the bearings are seized....and the motor will need to be replaced and is something you can do yourself. If the motor and fan turn freely then usually the ignition module that contains the relay is bad and will need to be replaced. This is also something you can do yourself if you transfer the wires one by one or label them. If you replace the ignition module you will need to make sure you get the exact replacement. There are many ignition modules used in several industries that range from pools to HVAC to industrial dryers.......they all look the same! Make sure you match the model#, the voltages, and the time durations!